 |
Automotive presses - Press technology | Ortlinghaus
These large flywheel presses are mainly used for the production of large and complex forming parts for automakers. The drivetrain system usually consists of hydraulically actuated, wet-running, multi-plate clutch-brake units. Ortlinghaus is also the preferred supplier of most worldwide press manufacturers and automakers.

Main drive - Automotive presses
Main drive locking clutch | Series 055
Transferring press ram weight to press frame at stationary press
According to DIN EN 692, the relevant safety standards for press engineering, a mechanical restraining device must be present in mechanical presses for repair work and work between the two halves of the tool. The Ortlinghaus linear motion lock from the series 055 is an approved restraining device according to the German employers’ liability insurance association. The linear motion lock is used to positively lock a shaft to the fixed housing of a clutch so that the shaft cannot rotate. This is particularly desirable for presses to ensure that the press ram will not move in an uncontrolled or unintended manner during servicing or maintenance work between the two halves of the die.

The Ortlinghaus ram locking mechanism enables a variable locking of the press ram in any position, with a short actuating time of about three seconds. The linear motion lock is matched to and integrated into the machine’s drivetrain. It is engaged or disengaged hydraulically. The state of the ram locking mechanism actuated by oil pressure, either locked or unlocked, is detected using inductive travel sensors and transmitted to the machine control unit.

- Torque: 11,000 - 100,000 Nm
- Outside diameter:480 - 900 mm
- Bore diameter:120 - 260 mm
- Length:195 - 325 mm
|
|
 |

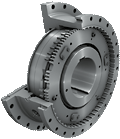 |
Hydraulical clutch-brake unit | Series 123
Hydraulically actuated, wet-running, high thermal load allowed
The hydraulically actuated clutch-brake units from the series 123 work exclusively with wet-running, oil-cooled plates with friction pairing steel/sinter.

The advantages of having a multi-plate construction and oil-cooled friction pairing steel/high-performance sinter in addition to actuation with pressure oil at 60 bar are seen in the product’s extraordinarily compact design and high operating efficiency. The series offer high torque, low moment of inertia and high switching speeds with a minimal need for maintenance. Model series 123 represent a good alternative to dry-running combinations. They operate in sealed housings which prevent leakage and keep switching noise to a minimum.

With these benefits, the clutch-brake units are suitable for a broad range of applications in press, shear press, and large press engineering as well as in embossing presses and drawing presses. The series was designed and constructed according to international safety regulations and approved by the German employers’ liability insurance association.

- Torque: 3,000 - 630,000 Nm
- Rotations per minute: 350 - 1,700 min-1
- Outside diameter: 199 - 1,180 mm
- Bore diameter: 58 - 375 mm
- Length: 135 - 650 mm
|
|

|

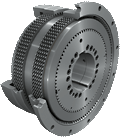
|
Rotary inlet | Series 086/087
Ortlinghaus has been manufacturing single and multi-channel rotary inlets for several decades and these are frequently supplied as accessories for air and oil actuated and also for oil cooled clutches. These tried and tested machine components for the feeding of air, pressurised oil and cooling oil into rotating shafts are standard products and are not only for use in conjunction with clutches.

In addition to this Ortlinghaus also develops and manufacturers rotary inlets to customers own requirementswhich cannot be met from standard products listed in the catalogue. It is thus possible for example to manufacture rotary inlets with up to eight channels with the channels being able to carry different media (air / oil; air / water). |

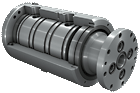 |
Drive control - Automotive presses

Control units | Series 086 - 392
- Fast filling and draining of the piston chamber of the clutch-brake unit
- Control of the clutching and breaking function of the clutch-brake unit
- Including safety valve

|

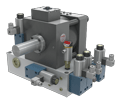 |
Pa.go System
Hydraulically actuated, wet-running clutch-brake system with mechatronic closed-loop control
Pa.go enables the precise closed-loop control of clutch-brake units in large presses. While such control brings considerable benefits during normal operations, it also helps to counter the impact of changes in operating conditions like temperature, wear, oil leakage etc.

Application
The speed-regulated servo pump produces the required operating pressure dynamically, allowing it to control acceleration and braking of the clutch-brake unit in a precise manner.

Safety
The press safety valve is monitored and actuated by the press’s safety controls.

Closed-loop control
The entire clutch and braking process is controlled by Pa.go Control, which matches the requested operating status with the current system pressure and Pa.go’s speed, then generates a target torque for the motor. The relevant parameters are transmitted to the servo controller via EtherCAT, which provides the electricity needed for the motor.

Diagnosis
The status variables of the regulation can be used to calculate plate wear, among other things. The wear variables can be called up on the display and are used for preventative maintenance. In addition, Pa.go Control records key data such as maximum pressure, acceleration time, braking time, reaction time, and clutch-brake unit switch time for each press stroke. The pressure and torque is recorded every set number of strokes in an oscilloscope graph so that the switches can be analyzed retrospectively.

Process reliability
A log file records any interruptions that occur as well as the total number of switches, allowing for preventive measures to increase the uptime of the press.
Productivity increase and equipment preservation
The innovative pressure regulation makes it possible to use the clutch and brakes quickly and smoothly. Thus, productivity is increased and the machinery is better preserved.
Features:
- Preventive maintenance
- Wear measurement
- Electronic slip control
- Error diagnosis
- Interface
- Diagnosis of CBU data
- Closed-loop control of Pa.go
- Convenient touch display
- SD card slot for data recording
- Various sensor and bus interfaces
Increasing machine readiness
Preventative maintenance enabled by qualitative wear recognition increases machine readiness on a long-term basis. The availability of the machine is thereby ensured, along with the overload safeguard, by means of calculations on the basis of the current heat load. |
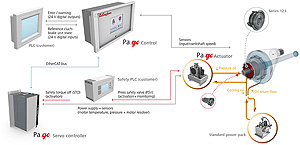 |
Conserving resources
The speed-controlled servo pump works efficiently and conserves resources.
 |

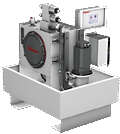
|
Diagnostic port
- Interface for connection measurement equipment
- Transmits speed-signals, pressure-signals and PSW-signals
 |

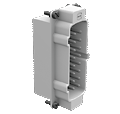
|
|
|